PanSolidification
The PanSolidification module is designed for the simulation of solidification behavior of multicomponent alloys under a variety of conditions with different cooling rates. It is an extension of the Scheil model taking into consideration of back diffusion in the solid, secondary dendrite arm coarsening, and the formation of eutectic structure. It is seamlessly integrated with the user-friendly Pandat Graphical User Interface (PanGUI) as well as thermodynamic calculation engine, PanEngine. The implementation of PanEngine guarantees reliable input data, such as chemical potential, phase equilibrium and mobility. . This module can predict the secondary dendrite arm spacing (SDAS), microsegregation, types and amounts of non-equilibrium phases in the solidification microstructure of multi-component alloys by incorporating back diffusion in the solidified primary phase, as well as the undercooling and dendrite arm coarsening during solidification.
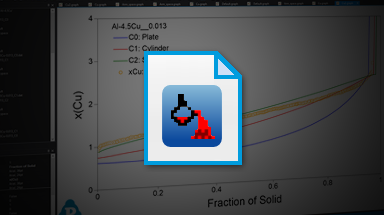
PanSolidification
- solidification path
- back-diffusion in the solid
- dendrite arm coarsening
- micro-segregation
Some Key Features of PanSolidification Module
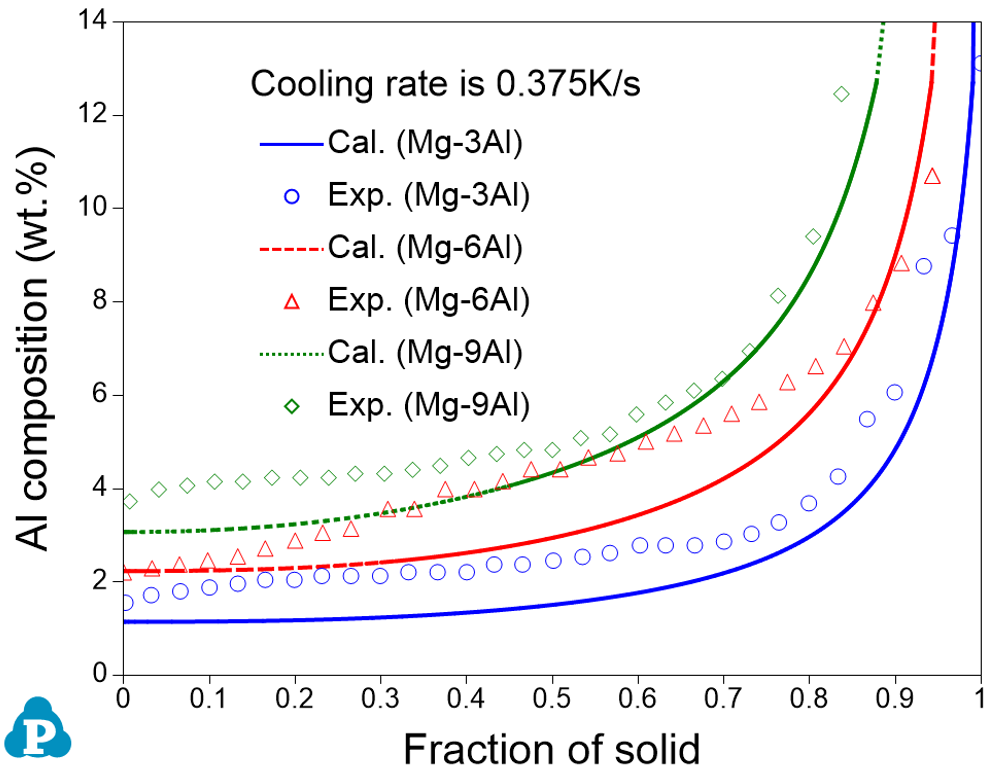
The simulated and measured AL composition profiles as a function of the fraction of primary α (Mg) phase for three magnesium rich alloys: Mg-3Al, Mg-6Al, and Mg-9Al (wt%) at the cooling rate of 0.375K/s.
- Integrated: seamlessly integrated with the user-friendly PandatTM Graphical User Interface (GUI) as well as thermodynamic calculation engine, PanEngine
- Advanced Models: Three models available for solidification simulation including Lever rule model (equilibrium), Scheil model (no diffusion in solid), and modified Scheil model taking into account of back diffusion in the solid and dendrite arm coarsening
- Three Geometry Models: plate, cylinder and sphere available
- Solidification Microstructure: predict the secondary dendrite arm spacing (SDAS), microsegregation, types and amounts of non-equilibrium phases of multi-component alloys under different cooling rates