Solutions for Magnesium alloys
There are a large number of commercial magnesium alloys of industrial relevance, including the Mg-Al based alloys, such as AZ, AE, AJ, AM, AS, and AX; Mg-Zn-Zr based alloys, such as ZK60; Mg-RE (rare earth)-Zn (EZ) alloys; and Mg-RE-Zr based alloys, such as WE. Due to the variations in chemistry and processing conditions, none of the handbooks can provide all the data that cover the entire composition range for each alloy with various processing conditions. With Pandat software and PanMg database, we can simulate variety of properties for the applications of magnesium alloys. Here we will use a few examples to demonstrate how one can use Pandat software and PanMg database to optimize the alloy chemistry and processing conditions to achieve the desired properties for magnesium alloys.
Application Examples
Al–Mn–Fe intermetallic formation in AZ91 alloys: Effects of impurity iron
The formation of AlMnFe intermetallic phases improves the corrosion resistance of Mg alloys. This isopleth section of (90.14-x)Mg-8.95Al-0.72Zn-0.19Mn-xFe calculated by PanPhaseDiagram module provides the information of Fe content on the formation of intermetallic phases. The black dashed lines indicate the change in liquid composition during Fe pickup at each holding temperature.
Please refer Peng et al. Intermetallics, 142 (2022) 107465 for details.
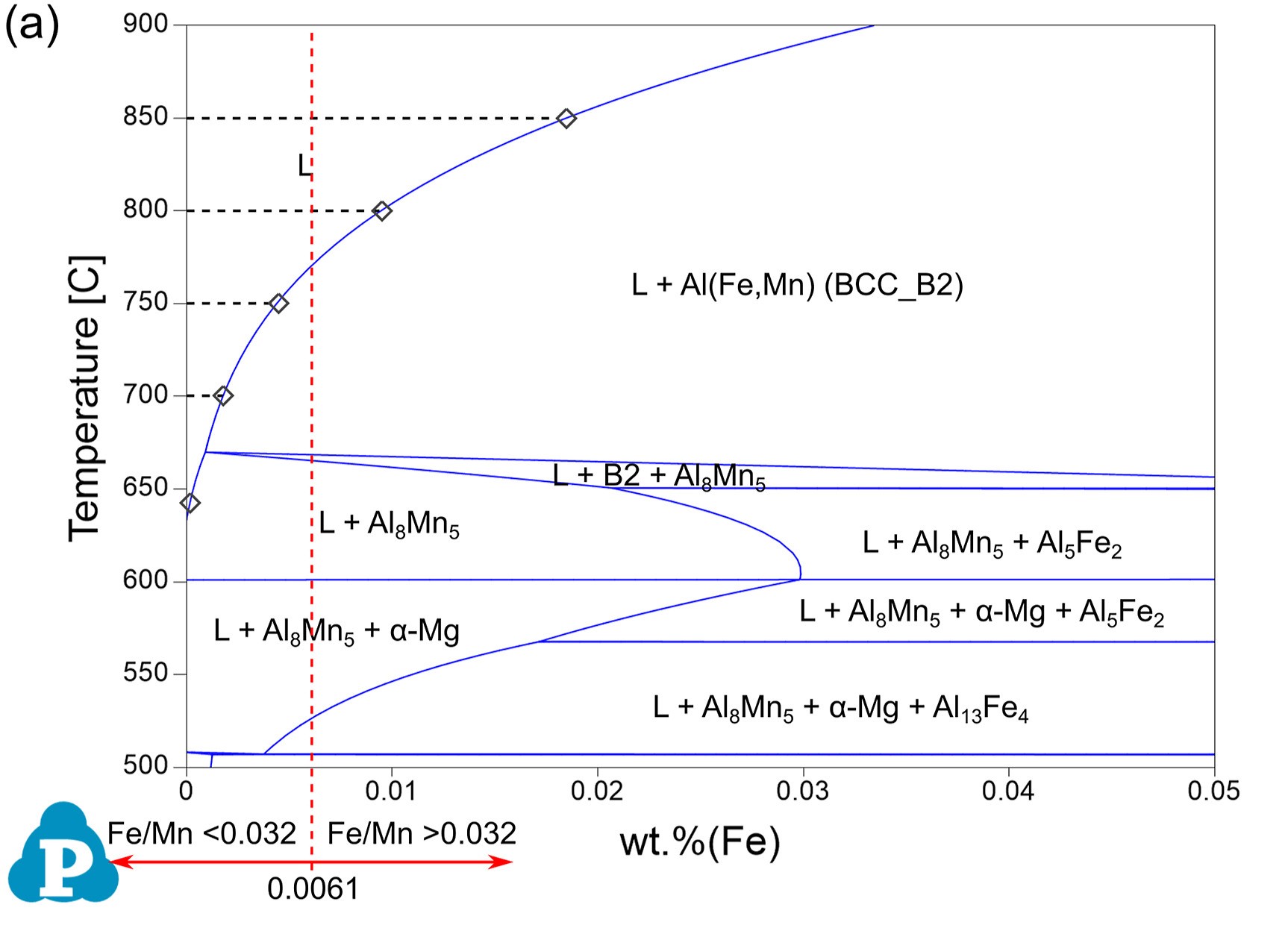
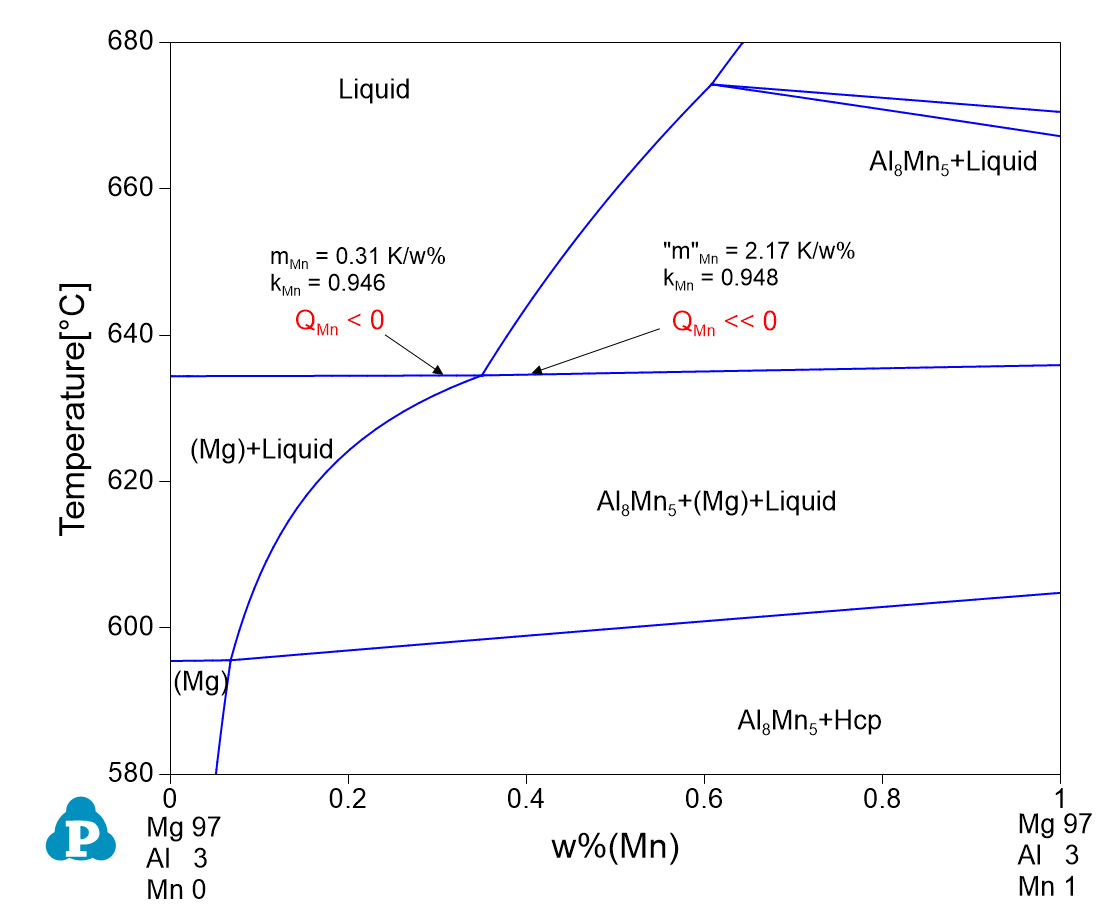
Grain growth restriction factor
The growth restriction factor Q is the key quantity in the description of the solutal effect on grain growth and grain refinement during solidification of alloys. The tradition way of obtaining Q value from liquidus gradient (mi) and partition coefficient (ki) fails in multicomponent systems. This figure shows an example of the negative Q value in Mg-Al-Mn system. On other hand, the true Q value of multicomponent alloys can be calculated in PanPhaseDiagram module based on the initial definition from constitutional supercooling. More details can be found in Schmid-Fetzer and Kozlov, Acta Mater., 59 (2011) 6133-6144.
Microstructural evolution of Mg alloys during solidification
The properties of cast Mg alloys are generally attributed to several microstructural parameters, such as grain size, primary dendrite arm spacing (PDAS), secondary dendrite arm spacing (SDAS), microsegregation of alloying elements, distribution/fractions of constituent phases, etc. The element distribution in the primary phase and the SDAS of Mg alloys under different cooling rate can be simulated in PanSolidification module. This figure shows the distribution of elements in (Mg) matrix in Mg-7Al-2Sn alloy with cooling rate of 55 K/s.
More details can be found in Zhang et al., J. Phase Equilib. Diffus., 40 (2019) 495-507.
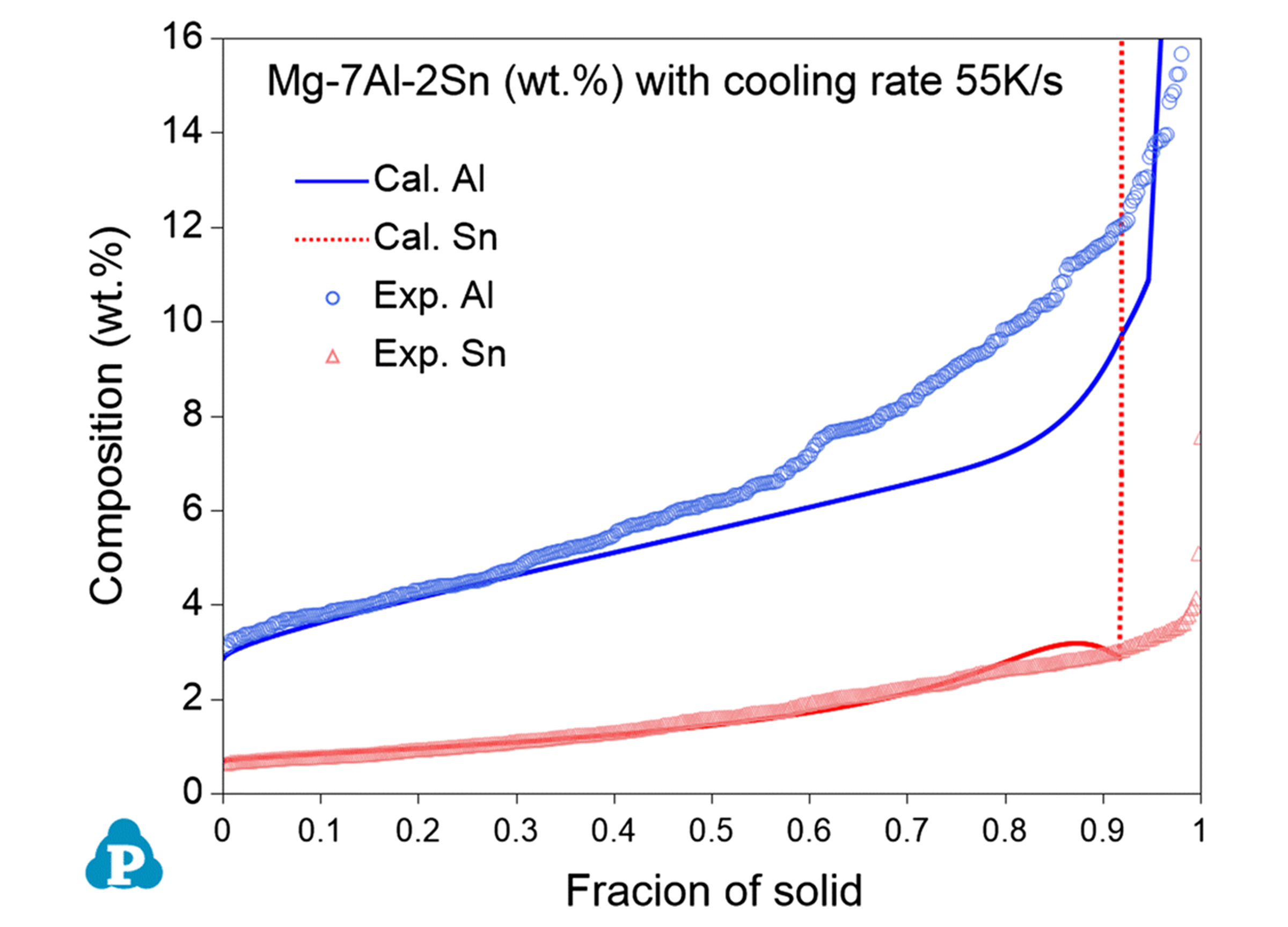
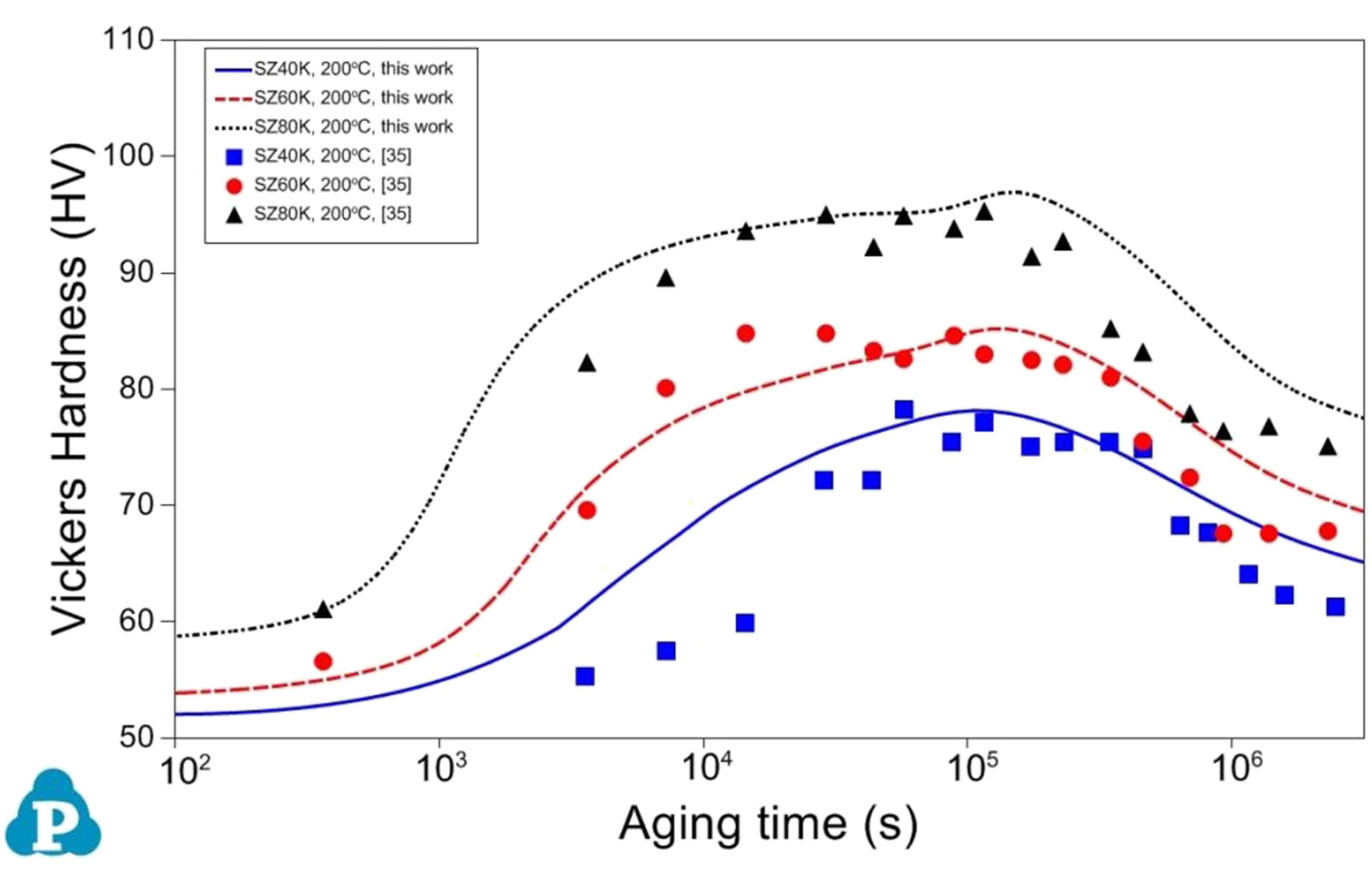
Precipitation hardening in Mg alloys
Precipitation hardening is one of the most important strategies for developing high strength Mg alloys. The precipitation behavior and age-hardening can be simulated in PanPrecipitation module. This figure shows the evolution of hardness of Mg-4Sm-0.4Zr-xZn (wt.%) alloys during ageing at 200 °C.
More details can be found in Xia et al. Acta Mater., 111 (2016) 335-347
Below are some other publications on Mg precipitation simulation:
Zhang et al. JOM, 66 (2014) 389-396
Sun et al. Magnesium Technology 2015, 289-293
Still have question? Contact us to find a solution for your applications.