Additive manufacturing of ultrafine-grained high-strength titanium alloys
Titanium alloys made by additive manufacturing have been used in applications in various industries. However, the intrinsic high cooling rates and high thermal gradient of the fusion-based metal additive manufacturing process often leads to the formation of columnar grains in titanium-based alloys, which is undesirable. Attempts have been made to optimize the processing parameters of additive manufacturing to promote equiaxed growth of titanium grains. In a recent publication, (Nature, 2019), Zhang and colleagues have successfully additive manufactured Ti-Cu based alloy specimens which exhibit fully equiaxed fine-grained microstructure. These specimens also demonstrated promising mechanical properties. In their work, thermodynamic calculations were employed to understand the difference between Ti-Cu based alloys and other Ti alloys, and explain the phenomena observed experimentally. The calculations include solidification pathways using Scheil–Gulliver model, and the growth restriction factor Q. Pandat software and PanTi database were used to perform these simulations.
The Figure shows Scheil simulations for Ti-8Cu, Ti-6Al-4V, and Ti-6Al-4V-0.5Fe (all in wt%) using Pandat software and PanTi database. As indicated in the paper of Zhang et al., although the solidification range for Ti-Cu alloys is large, no cracking was observed. This could be explained by the cracking susceptibility Index (CSI) developed by Kou (Acta Materialia, 2015).
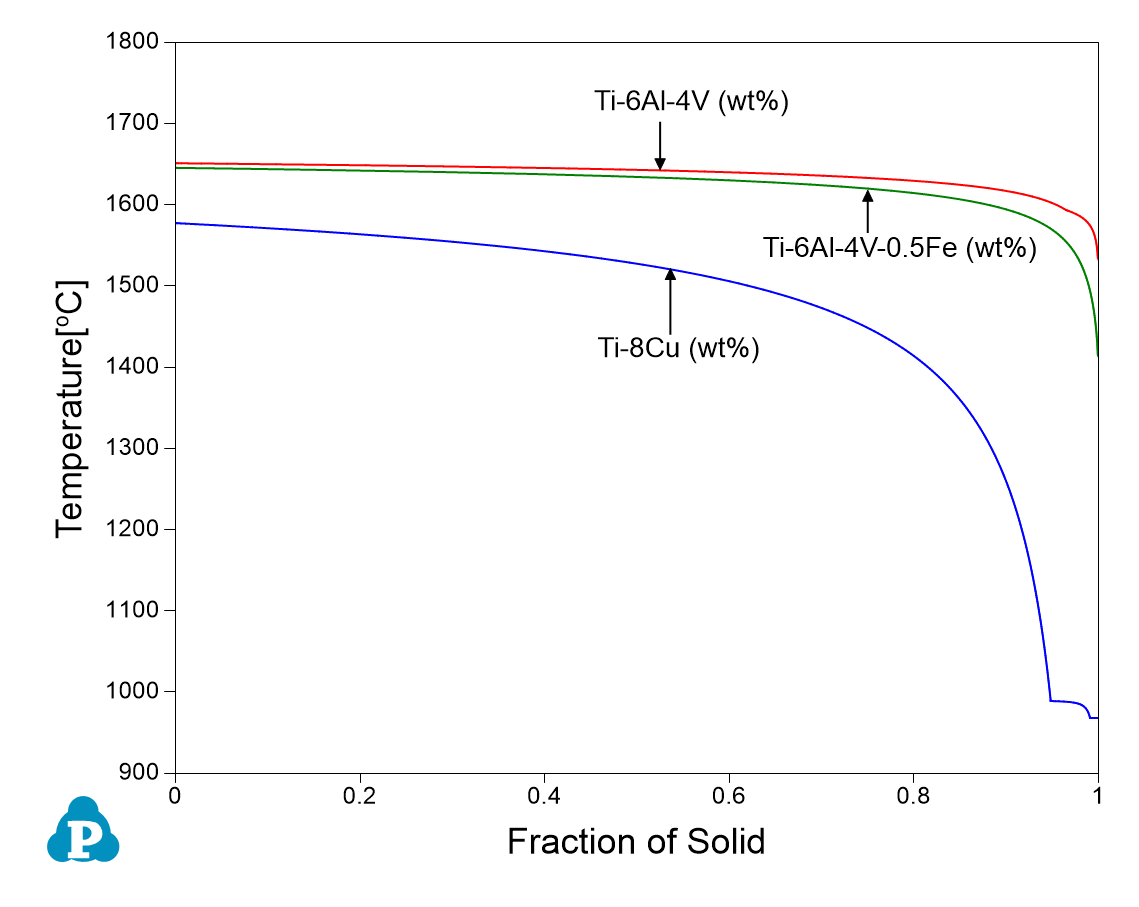
Ref:
D. Zhang, D. Qiu, M.A. Gibson, Y. Zheng, H.L. Fraser, D.H. StJohn, M.A. Easton, Additive manufacturing of ultrafine-grained high-strength titanium alloys, Nature 576 (2019) 91-95. doi:10.1038/s41586-019-1783-1.
S. Kou, A criterion for cracking during solidification, Acta Mater., 88 (2015) 366-374. doi:10.1016/j.actamat.2015.01.034
Publications related to different topics